Understanding the Dynamics of China Plastic Injection Moulding
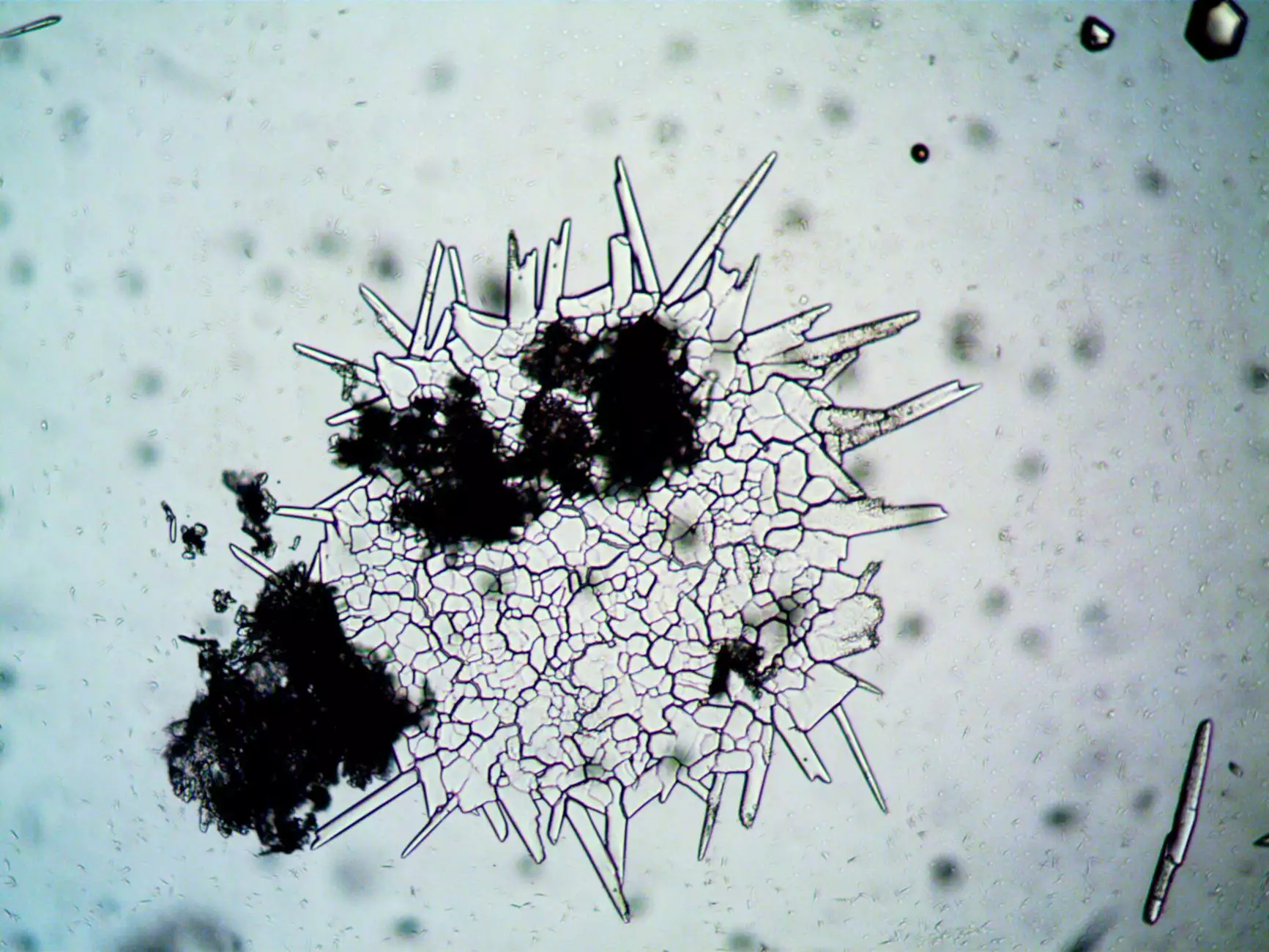
In today's ever-evolving industrial landscape, China plastic injection moulding stands as a pillar of modern manufacturing. This technique revolutionizes the way companies produce plastic products, optimizing both efficiency and quality. In this comprehensive guide, we delve deep into the intricacies of plastic injection moulding, its benefits, the process, and why choosing reputable suppliers like deepmould.net can elevate your business.
What is Plastic Injection Moulding?
Plastic injection moulding is a manufacturing process that involves the creation of parts by injecting molten plastic into a mould. The versatility of this technique allows it to produce a wide range of objects, from small components to large housings. The process involves several steps:
- Material Selection: Choosing the right type of plastic for the product.
- Heating: Melting the plastic to a liquid form.
- Injection: Introducing the molten plastic into the mould under high pressure.
- Cooling: Allowing the plastic to solidify within the mould.
- Demoulding: Removing the solidified product from the mould.
Benefits of China Plastic Injection Moulding
The advantages of utilizing China plastic injection moulding are numerous, making it a preferred method in various industrial applications.
1. High Efficiency
Once the mould is created, the production process is exceptionally fast. Parts can be produced in rapid succession, enabling large volumes of products within a short timeframe.
2. Excellent Reproducibility
One of the primary advantages is the ability to produce identical parts repetitively, ensuring consistency in quality and performance. This reproducibility is crucial in fields like automotive manufacturing, where precision is vital.
3. Cost-Effectiveness
Although the initial cost of producing moulds can be high, the reduced cost per part in mass production compensates for this. Businesses can enjoy substantial savings while benefiting from the scale of production.
4. Design Flexibility
Injection moulding allows for intricate designs and complex shapes that may be challenging to achieve through other manufacturing methods. This adaptability facilitates innovation and creativity in product development.
5. Material Variety
A wide range of thermoplastics and thermosetting plastics can be utilized in the process, allowing manufacturers to choose materials that best suit the end-use application. This variety ensures that products can possess desirable characteristics such as durability, flexibility, and resistance to heat or chemicals.
The Moulding Process Explained
To fully grasp the potential of China plastic injection moulding, it is essential to understand the process in detail. Here's a step-by-step breakdown:
1. Design and Prototyping
Before production can begin, an engineer designs a component which may go through iterative prototyping. Computer-aided design (CAD) software is often used for precision and accuracy. It’s important to optimize the design for manufacturability.
2. Manufacturing the Mould
The mould itself is custom-made, usually from steel or aluminum. The complexity of the design influences the cost and time required for this process. High-quality moulds can last for thousands of cycles.
3. Setting Up the Injection Moulding Machine
The machine is calibrated to inject plastic at the correct temperature and pressure. Details including the temperature of the nozzle and the mould will vary depending on the material used.
4. Injection Phase
During this phase, the melted plastic is injected into the mould at high speed. The pressure helps in filling the mould completely, ensuring that every detail is captured.
5. Cooling Phase
Once the mould is filled, the plastic is allowed to cool and solidify. Cooling times vary based on product size and material. Efficient cooling is critical, as it affects the cycle time and overall efficiency of production.
6. Unloading the Product
After solidification, the mould is opened, and the finished product is ejected. This step may involve additional processes such as trimming or surface finishing.
Types of Plastic Injection Moulding
There are various types of plastic injection moulding techniques utilized in the industry. Understanding these can help businesses choose the right method for their projects:
- Single-Material Moulding: Most common, using one type of plastic to create a single part.
- Multi-Material Moulding: Allows the simultaneous use of different materials to create complex parts with diverse properties.
- Overmoulding: Involves injecting a second material over an existing part to enhance functionality or aesthetics.
- Insert Moulding: Involves placing materials, such as metal inserts, into the mould before the plastic is injected, creating strong composite components.
Choosing the Right Manufacturing Partner
When selecting a supplier for China plastic injection moulding, there are critical factors to consider:
1. Experience and Expertise
Look for companies with a proven track record in the industry. Experienced manufacturers can guide you through the design and production processes and address potential challenges.
2. Quality Standards
Ensure that the manufacturer adheres to international quality standards and possesses the necessary certifications. Quality assurance practices are crucial for maintaining product integrity.
3. Customization Capabilities
Every project is unique. A capable manufacturer will work closely with clients to modify designs and processes to meet specific needs. Custom solutions can significantly impact the success of the project.
4. Cost and Value
While cost is a critical factor, it shouldn’t be the only one. Evaluate the overall value, including quality, customer service, and support offered by the manufacturer. Sometimes, paying slightly more can yield significant long-term benefits.
5. Technological Advancements
Choose a supplier that invests in the latest technologies. Advanced equipment can improve efficiency and product quality and may offer additional services such as rapid prototyping or advanced colour matching.
Conclusion: The Future of Plastic Injection Moulding in China
As industries continue to innovate, the demand for high-quality plastic products manufactured through China plastic injection moulding will only grow. Companies like deepmould.net are at the forefront of this advancement, providing robust manufacturing solutions that integrate quality, efficiency, and modern design capabilities. Understanding the benefits and intricacies of this process is essential for any business looking to thrive in today's competitive market.
Investing in reliable manufacturing processes can lead to sustainable business growth, innovative product development, and a stronger position in the marketplace. The future is bright for businesses that harness the potential of plastic injection moulding, especially when done in partnership with experienced professionals in China.