Exploring Metal Die Casting Manufacturers: A Comprehensive Guide
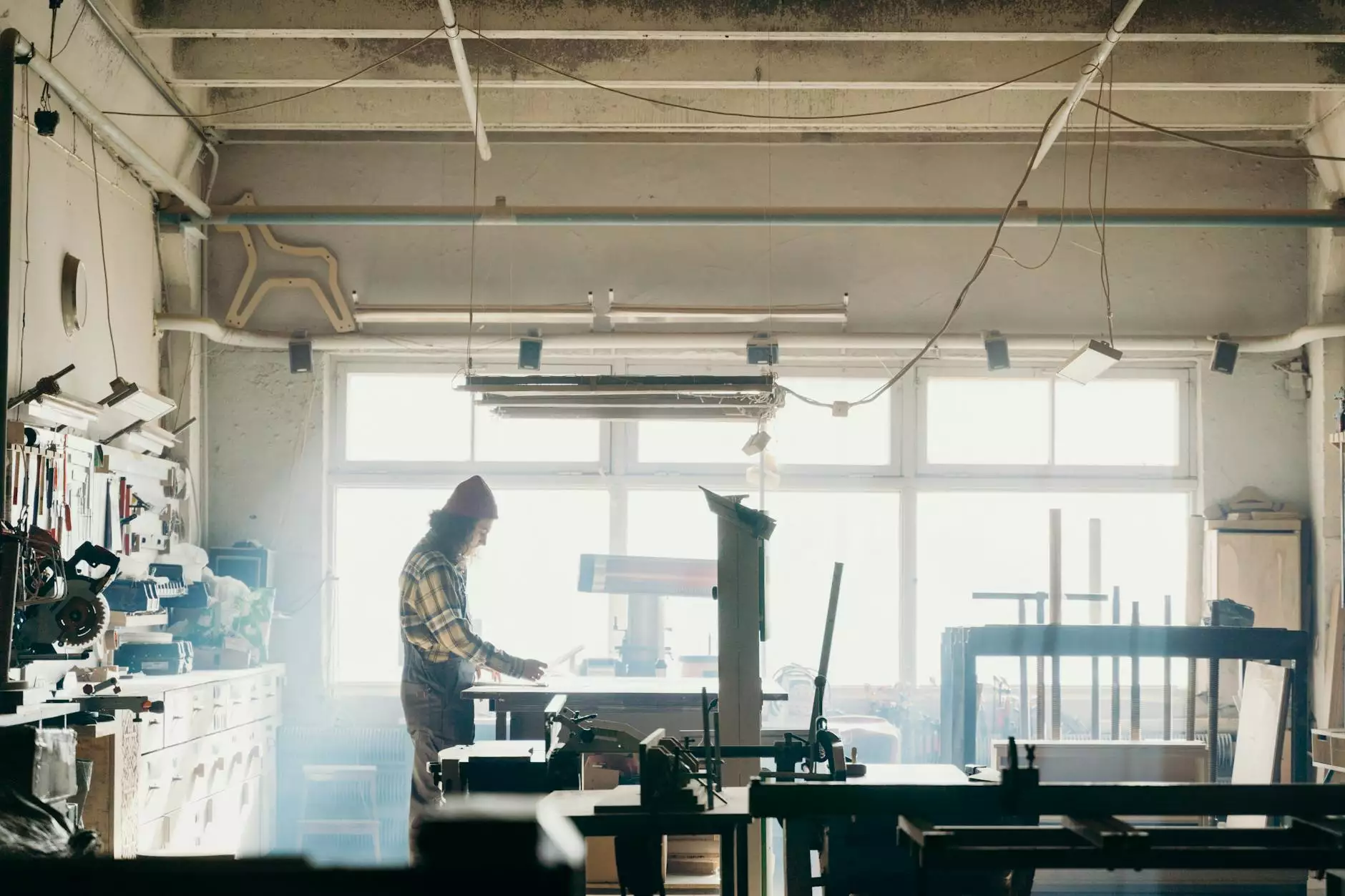
In the realm of manufacturing, few processes are as crucial to the creation of metal components as die casting. This method allows for the production of complex and intricate designs that can withstand the rigors of various industries. Understanding the capabilities, advantages, and selections available through metal die casting manufacturers can elevate your production capabilities. This article dives deep into the world of die casting, focusing on the significant aspects that underline its importance in the manufacturing sector.
What is Metal Die Casting?
Metal die casting is a process where molten metal is injected under high pressure into a mold cavity. This method is favored for its ability to produce large volumes of parts with high dimensional accuracy and smooth finishes. The two primary types of die casting are:
- High-Pressure Die Casting: Involves forcing molten metal into a mold at high pressure, resulting in excellent surface finish and intricate details.
- Low-Pressure Die Casting: This method uses lower pressure and is typically used for larger parts, offering benefits in terms of material usage and cost efficiency.
Advantages of Metal Die Casting
Engaging with reputable metal die casting manufacturers offers numerous benefits, making this manufacturing process a go-to choice for many industries. Here are some key advantages:
- High Precision and Repeatability: Die casting produces parts that are consistent in dimensions, ensuring that each piece meets strict specifications, essential for high-quality finished products.
- Complex Geometries: The intricacy of designs achievable through die casting is unparalleled. Manufacturers can create complex shapes that would be difficult or impossible to produce with other methods.
- Efficient Production: Once the die is created, production can proceed rapidly with little downtime, allowing for quick turnaround times for large orders.
- Enhanced Surface Finish: The smooth surfaces of die-cast parts often require little to no secondary finishing, reducing the overall production time and costs.
- Material Versatility: Die casting works well with numerous alloys, including aluminum, zinc, and magnesium, allowing manufacturers to choose the best material for their product needs.
Choosing the Right Metal Die Casting Manufacturer
When it comes to selecting a metal die casting manufacturer, thorough research is key. Here are some factors to consider:
- Experience and Expertise: Select manufacturers with proven expertise in die casting and a portfolio of successful projects across various industries.
- Quality Standards: Ensure that the manufacturer adheres to stringent quality control measures and certifications, such as ISO, which can assure reliability in product quality.
- Technology and Equipment: Evaluate the manufacturing capabilities and technology employed by the manufacturer. Advanced machinery can enhance production efficiency and accuracy.
- Customer Service: Good communication and responsive customer service are essential for a successful partnership.
- Competitive Pricing: While cost should not be the sole factor, it is vital to understand the pricing structures of different manufacturers to ensure you are getting value for your investment.
Applications of Die Casting in Various Industries
The versatility of metal die casting allows it to find applications across multiple sectors:
- Aerospace: Die casting provides lightweight, durable parts essential for aircraft performance and fuel efficiency.
- Automotive: Many automotive components are die-cast, including transmission cases and engine components, improving vehicle performance and reliability.
- Consumer Electronics: The housings and components of electronic devices often employ die casting for both weight and aesthetic appeal.
- Medical Devices: Precision is paramount in the medical field, making die casting flawless for producing intricate parts for various medical devices.
- Industrial Equipment: Heavy machinery often relies on robust, die-cast parts that can withstand harsh conditions.
Trends in Metal Die Casting
The landscape of die casting manufacturing is ever-evolving. Here are some trends reshaping the industry:
- Sustainability Initiatives: Manufacturers are adopting eco-friendly practices, including using recyclable materials and reducing waste during production.
- Automation and Smart Manufacturing: The integration of automation technologies enables higher precision, reduced errors, and accelerated production cycles.
- 3D Printing for Dies: 3D printing technology is being used to create more complex dies, enhancing design capabilities and reducing lead times.
- Alloy Innovations: Research into new alloys and materials is expanding the possibilities of die casting, with custom formulations being developed for specific applications.
Conclusion: Elevate Your Business with Quality Die Casting
Engaging with skilled metal die casting manufacturers can transform your production capabilities. By leveraging the advantages of die casting, businesses can achieve cost-effective production, high-quality components, and faster turnaround times. Understanding the nuances of this process, including the selection of the right manufacturer and staying updated on industry trends, ensures you remain competitive in your field.
Whether you are in the automotive, aerospace, or consumer electronics sector, the integration of die casting into your manufacturing process can lead to significant innovations and improvements. By prioritizing quality and collaboration with experienced manufacturers like DeepMould.net, your business can achieve its goals in today’s demanding market.
For more information on how DeepMould.net can help you with your die casting needs, visit our website or contact us directly. With our commitment to excellence and customer satisfaction, we stand ready to assist you in all your metal fabrication projects.