Understanding Plastics Molding: A Comprehensive Guide for Businesses
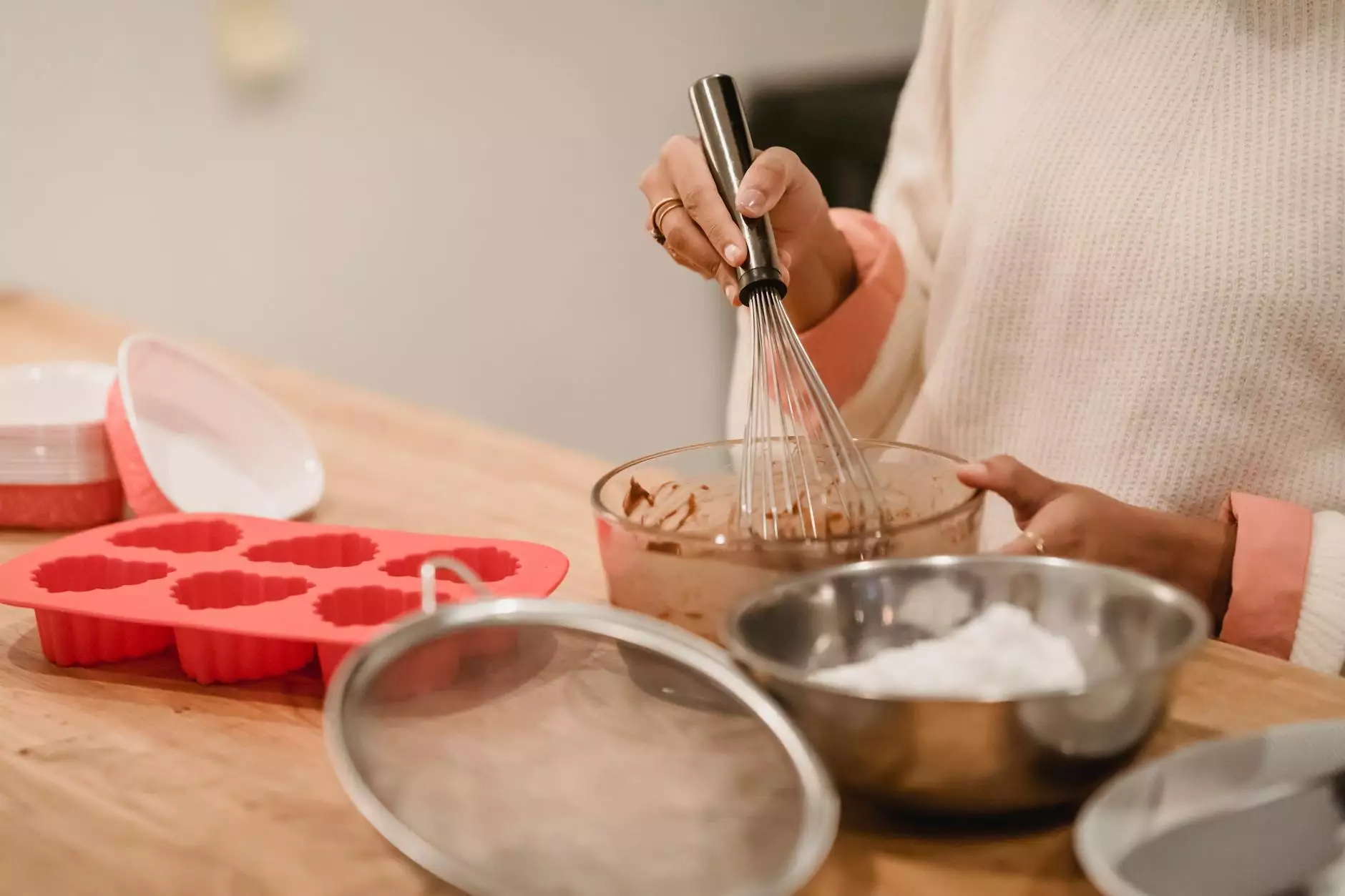
Plastics molding is a transformative process that has reshaped the manufacturing landscape. In this extensive guide, we will delve into its intricate workings, applications, and its significance, particularly for businesses engaged in metal fabrication like DeepMould. By the end of this article, you will have a clear understanding of the nuances of plastics molding and its pivotal role in modern manufacturing.
What is Plastics Molding?
Plastics molding refers to the various processes used to shape plastic materials into desired forms. It involves the heating of plastic, followed by the injection or shaping of that plastic into molds to create specific designs. This method is highly favored for its versatility, efficiency, and the wide range of products it can produce.
Types of Plastics Molding Processes
There are several methods of plastics molding, each suitable for different applications. Below are the most commonly used types:
- Injection Molding: Involves injecting molten plastic into a mold, where it cools and solidifies into the final product.
- Blow Molding: Used primarily for hollow objects. It involves inflating heated plastic into a mold.
- Rotational Molding: A method where plastic is heated and rotated to coat the mold’s interior, producing hollow items.
- Compression Molding: Involves placing plastic in a heated mold, and then applying pressure to form the desired shape.
- Thermoforming: In this process, sheet plastic is heated until pliable and then formed over a mold.
Benefits of Plastics Molding for Businesses
Plastics molding offers numerous advantages for manufacturers and businesses alike, especially in the realms of efficiency and cost-effectiveness:
- Cost Efficiency: Mass production through molding reduces the cost per unit significantly.
- Design Flexibility: Molding allows for intricate designs and customization, providing businesses with a competitive edge.
- Durability: Products made through molding are often robust and long-lasting, enhancing customer satisfaction.
- Reduced Waste: Advanced molding techniques minimize waste materials, contributing to environmental sustainability.
- Rapid Production: Compared to many other manufacturing processes, molding can facilitate rapid production cycles.
The Role of Plastics Molding in Metal Fabrication
For companies involved in metal fabrication like DeepMould, understanding the integration of plastics molding with metal processes is essential. The use of plastic components can significantly enhance the overall functionality of metal products.
Integration of Plastics and Metals
The combination of plastics and metals often leads to innovative products that leverage the strengths of both materials. This hybrid approach can lead to:
- Weight Reduction: Using plastic in place of metal in non-structural applications can reduce overall product weight.
- Corrosion Resistance: Plastics can provide protective barriers against corrosion, extending the lifespan of products.
- Improved Aesthetics: Plastics can be easily colored or textured, enhancing the visual appeal of metal products.
Applications of Plastics Molding Across Industries
Plastics molding is versatile and its applications span across numerous industries:
- Automotive Industry: Used for dashboards, instrument panels, and various exterior and interior components.
- Consumer Electronics: Essential for producing casings, connectors, and internal elements of electronic devices.
- Medical Devices: Molding is critical for creating sterile, disposable items and components for complex medical machinery.
- Consumer Goods: Everything from toys to household items often relies on efficient plastics molding processes.
Choosing the Right Plastics Molding Partner
Selecting the right partner for your plastics molding needs is crucial for the success of your projects. Here are key considerations when choosing a provider:
- Experience and Expertise: Look for a company with a solid track record and expertise in your specific industry.
- Quality Assurance: Ensure that the partner practices rigorous quality control to meet industry standards.
- Technology and Equipment: The latest technology can influence the efficiency and quality of the molding process.
- Customer Support: A competent partner should provide excellent support throughout the production process.
The Future of Plastics Molding
As technology evolves, so does the landscape of plastics molding. Several trends are shaping the future:
- 3D Printing Integration: The fusion of 3D printing with traditional molding technologies is fostering greater customization possibilities.
- Biodegradable Plastics: As environmental concerns grow, the use of sustainable materials in molding processes is on the rise.
- Smart Manufacturing: Automation and smart technologies are being introduced to improve efficiency and reduce production times.
Challenges in Plastics Molding
Despite numerous advantages, businesses must navigate several challenges in the plastics molding process:
- Material Selection: Choosing the right type of plastic is essential for achieving product durability and performance.
- Tooling Costs: Initial investments in molds and tools can be substantial, especially for complex designs.
- Waste Management: It’s vital to have a strategy in place to manage and recycle scrap materials effectively.
Conclusion
In conclusion, plastics molding is an essential process for modern manufacturing that offers remarkable flexibility, efficiency, and cost-effectiveness. For businesses, particularly those involved in metal fabrication such as DeepMould, understanding and leveraging the benefits of plastics molding can lead to innovative products and satisfied customers. As you navigate through the complexities of manufacturing, staying informed about the advancements in plastics molding will serve as a significant advantage in this competitive industry.
Explore the potential of plastics molding today, and take your business to the next level!